Projects
Projects
Our Portfolio
Explore some of our completed work
Categories
All Projects
Chevron Petro-chemical Plant
Plant Modeling from 3D Scan Data
Plant modeling from 3D scan data refers to the process of creating a digital representation or model of a physical plant or facility using three-dimensional (3D) scanning technology. 3D scanning involves capturing the physical dimensions, shape, and surface details of an object or environment using specialized scanners or cameras.
Bloodhound SSC
Digital Terrain Model of the Land Speed Record Track at Hakskeenpan
We were involved in this project together with two other South African survey companies to survey the proposed track at Hakskeenpan and represent the data in a digital format.
We were responsible for calculating a 1m x 1m structured grid of elevations over the entire area of the track (16km x 900m) from an unordered point cloud obtained using a combination of Precise Leveling and Mobile Laser Scanning.
Heritage Building Survey
3D Scanning of a Heritage Building at a Wine Estate for Architectural Renovation
This scanning process utilizes specialized scanners or cameras to record the physical dimensions, textures, and intricacies of the building’s interior and exterior. The purpose of this scanning is to create a highly accurate digital replica or model of the heritage building.
By obtaining a precise 3D model, architects and renovation experts can gain a comprehensive understanding of the building’s existing structure and design elements. This allows them to plan and visualize potential renovation or restoration projects more effectively.
They can assess structural integrity, identify areas requiring repairs or improvements, and experiment with different design concepts virtually.
Barnard Hypercar
3D Laser Scanning and Surface Modeling for Carbon Fibre Tooling / Mold Making.
We did 3D Laser Scanning (LiDAR) of the Hypercar to produce various parts out of Carbon Fibre. One of the Intakes were scanned and modeled for the tooling / mold making process.
The surface modeling was done in such a way that the newly fabricated Carbon Fibre body interfaces perfectly with the existing Chrome parts and now the intake can be repeatedly re-produced, accurately and efficiently.
We were also asked to design a new Front Splitter. Having 3D CAD Design Staff in house, we are able to produce multiple Design Concepts and Realistic Renders, from which clients can pick their favourites for further development.
55ft Catamaran
B-Spline / NURBS Surface Modeling from 3D Scan Data for Tooling / Mold Making
B-Spline/NURBS surface modeling from 3D scan data for tooling/mold making involves using B-Spline or Non-Uniform Rational B-Spline (NURBS) techniques to create smooth and accurate digital models of surfaces derived from 3D scan data. B-Splines and NURBS are mathematical representations that allow for flexible and precise control over the shape and curvature of surfaces.
In the context of tooling and mold making, these models are utilized to design molds and tooling components with complex geometries. By converting the 3D scan data into B-Spline or NURBS surfaces, engineers and designers can manipulate and refine the digital model to ensure optimal fit, functionality, and manufacturability of the tools and molds.
This process helps streamline the tooling and mold making process, resulting in more efficient production and higher-quality end products.
Carrier Body As-Built Survey
Precise Survey of Carrier Body for a Diamond Mining Vessel
We performed a precise as-built survey of a newly constructed steel structure for a well known steel fabricator in Cape Town. We were required to certify whether specified geometry is within design tolerances before transporting the new part from the factory to the Vessel in the Cape Town docks.
We created a control network with many redundant survey observations and after computing the network with a Least Squares Adjustment it was confirmed that most of our observations could be repeated with a precision better than 0.7mm (With the largest misclosure being 1.4mm).
The Carrier body was transported to the Harbour and we were informed that the fit-up of the part was successful.
Chemical Plant
Laser Scanning (LiDAR) and 3D Modeling of a Chemical Plant in Kwazulu Natal
We were contracted by a Plant in Kwazulu Natal to do 3D Laser Scanning of a specified area. We complied with all the safety standards and mobilised a scanning team to the Plant. The Laser Scanning was controlled using Precise Engineering Survey techniques and all Scan Data was registered together with a Standard Deviation of 2mm.
The contract specified that all Piping, Steelwork, Equipment and Utilities be modeled to a Standard Deviation of 5mm. We have streamlined workflows to extract and model Steelwork and Piping from the Point Cloud using Standard Libraries, so almost everything in the Model is to specification. Our team is very experienced and creative and we model custom objects like Vessels and Equipment as an accurate representation of the real world object.
We noticed that the concrete floor was not level (with height differences up to 200mm) to allow for drainage in the area where we were working.
We modeled the Organic shape of the Concrete Slab with a Standard Deviation of 5mm in Height and this allowed for accurate clash detection and future design with tight tolerances.
NMPP Tanks As-Built Survey
Deformation Analysis from Laser Scanning
We used custom in-house software to analyse and compare the surfaces of newly constructed tanks with design standards.
Masses of unordered Laser Scanning data had to be converted into a more convenient format by best fitting a Cylindrical Grid structure onto the surface of the tanks. We generate various reports to show deviations at each grid point when compared to the API 650 Standard.
Rivaero Gyrocopter
3D Laser Scanning and Modeling for Carbon Fibre Tooling / Mold Making
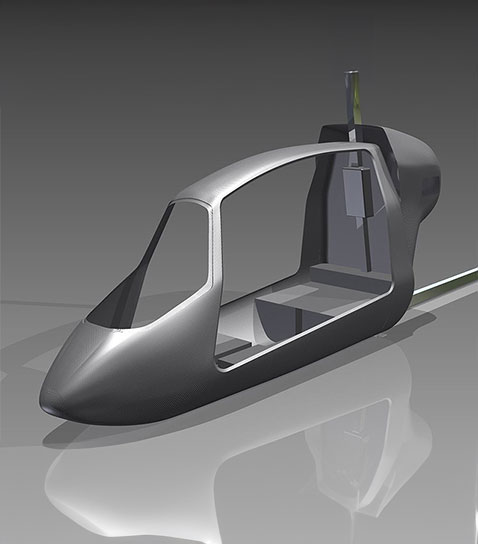
Austin Healey
3D Laser Scanning and Modeling for Carbon Fibre Tooling / Mold Making
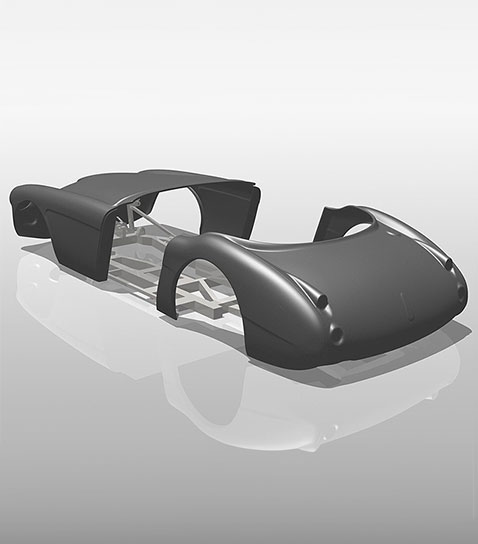
105ft Modern Superyacht
3D Laser Scanning and Modeling for Carbon Fibre Tooling / Mold Making
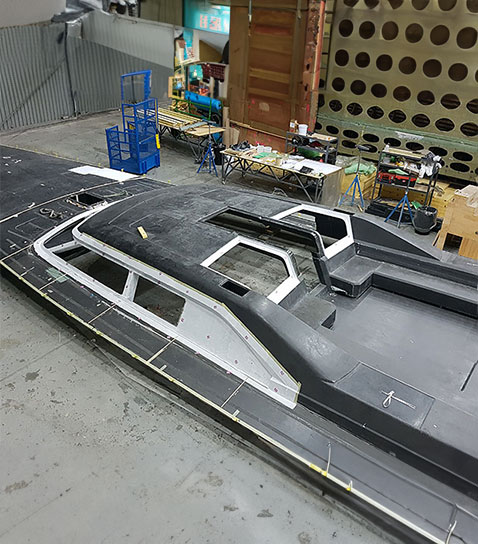
Nuclear Power Station
3D Modeling from Scan Data according to custom client supplied specifications
3D modeling from scan data according to custom client-supplied specifications for a nuclear power station involves using 3D scanning technology to capture the existing structures and equipment within the power station. The scan data is then utilized to create a digital 3D model that is customized based on the specific requirements and specifications provided by the client, facilitating accurate visualization, analysis, and planning for maintenance, upgrades, or other operational needs within the nuclear power station.
County Ford Kuils River
Stakeout Survey work for Civil Construction
This involves using surveying techniques to mark and locate specific points and positions on the construction site according to the design plans. This process ensures that the construction activities align with the intended layout and dimensions, aiding in the accurate placement of structures, foundations, utilities, and other elements during the construction process.
Carbon Fibre SUP Board
Surface Modeling for Tooling / Mold Making
We were approached by a Carbon Fibre company to assist on a Stand Up Paddle Board project. They had received data for a board that they wanted to manufacture out of Carbon Fibre, but the data format was not compatible with their manufacturing process.
We had to manually re-model the entire board fixing minor design characteristics of the board and changing the format to something that is better suited to their Tooling Process.
The project was a success and last time we visited the workshop the molds were ready and they were about to start laying the Pre-Preg Carbon Fibre Fabric into the mold.
Blacksmith Forge
3D Laser Scanning and Surface Modeling for Mold Making / Sand Casting
3D laser scanning and surface modeling for mold making/sand casting involves using laser scanning technology to capture the intricate details and geometry of an object or component. The scan data is then used to create a digital 3D model that serves as a precise reference for designing molds or patterns used in sand casting processes, ensuring accurate reproduction of the object in the casting process.